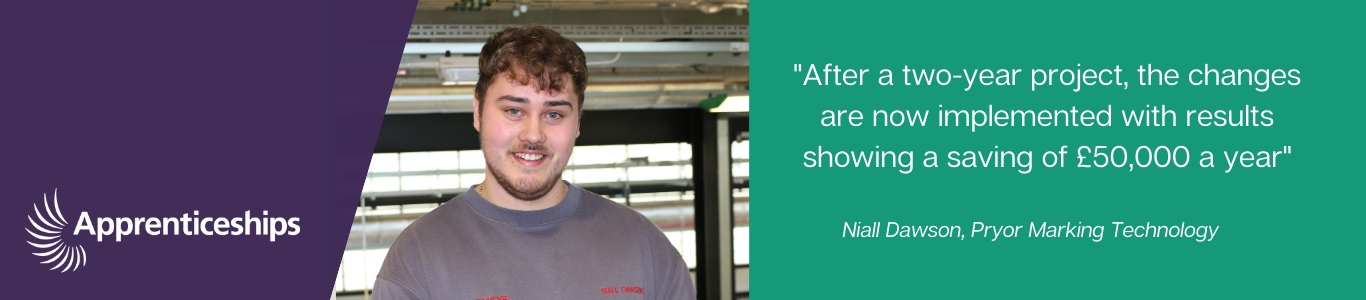
NIALL DAWSON - ACHIEVING £50K A YEAR PRODUCTION SAVINGS
Niall Dawson, age 21, Technical Support Apprentice at Pryor Marking Technology, a company designing and manufacturing intelligent marking, identification and code reading solutions based in Sheffield.
Niall completed his apprenticeship with the AMRC Training Centre says one his finest hours during that time was being lead designer in Pryor’s first wave implementation of dedicated assembly stations for standard products.
Assembly efficiencies made by Niall are saving his employer £50,000-a-year and slashing product build time by more than 60 per cent, from 3.5 hours down to just one hour.
Nat Russhard, Business Improvement Manager at Pryor Marking Technology, said Niall is the company’s first Technical Apprentice and his contribution to the organisation has been ‘truly remarkable’ in many ways.
“Niall has shown a flexibility to work across all areas of the business from shop floor to top floor. The practical skills he has picked up from a hands-on approach has helped significantly in providing outstanding cost savings to his re-engineered design of a standard product.
“He is a very important part of the Pryor organisation. His contribution, delivery and results speak for themselves. He has promoted and demonstrated the merits of the AMRC Training Centre apprenticeship scheme throughout the company.”
The project began with Niall looking at the assembly time of a standard product that was notoriously difficult to assemble with a right first time falling as low as 70 per cent.
“When looking at the bill of materials I quickly noticed some high cost parts that seemed very over-engineered for their function. Many colleagues within the fitting department had commented on the product taking multiple attempts to get right and this adds a lot of time on to the build,” says Niall.
“After a two-year project, the changes are now implemented with results showing a saving of £50,000 a year along with more than a 60 per cent reduction in the time it takes to build each product – the timescale being 3.5 hours down to one hour. It’s still early days but ‘Right First Time’ yield is now back where it should be at 100 percent. A planned follow up process will take place later this year to check compliance to the Standard Operating Procedure and to study any feedback for further improvements.
Niall is fully integrated into the design team at Pryor, working on sales orders and standard product development alongside five other fully qualified designers. He works independently on projects, tapping into the knowledge and experience of the experts around him to develop his core design skills. He added: “I am at a point now where I can support my own weight in the business.”
He is also part of the team developing Pryor’s approach to Industry 4.0 – the adoption of digital industrial technologies to create smarter, connected factories.
Nikki Jones, director of the AMRC Training Centre, said Niall is a shining example of the success that can be achieved through apprenticeships and of the benefits employers can reap by taking on an apprentice.
“Niall is an absolute credit to the AMRC Training Centre and to his company. During his apprenticeship, and beyond, he has displayed the right attitude, passion and commitment that companies are crying out for in manufacturing and engineering.”
Find out more about The University of Sheffield AMRC Training Centre at www.amrctraining.co.uk
Find out more about Pryor Marking Technology at www.pryormarking.com